Shitsurindo and ZOZO NEXT Launched Collaborative Research on New Lacquer Techniques
KOGEI Topics VOL.19
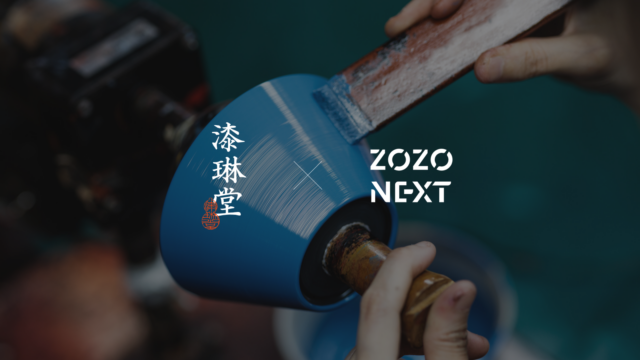
VOL.1-19
Update
VOL.1-17
Update
VOL.1-43
Update
VOL.1-2
Update
VOL.1-3
Update
VOL.1
Update
VOL.1-7
Update
VOL.1-32
Update
VOL.1-26
Update
VOL.1-12
Update
VOL.1-3
Update
VOL.1
Update
We share a variety of information and perspectives on Japanese crafts, including exhibition information and interviews.
KOGEI Topics VOL.19
New Products VOL.17
Featured Exhibitions & Events VOL.43
KOGEI Topics VOL.18
Apr 5 – Jun 22, 2025
SEIKADO BUNKO ART MUSEUM
Apr 8 – May 6, 2025
The Gotoh Museum
Apr 11 – Jun 15, 2025
Kyoto City KYOCERA Museum of Art
Apr 12 – Jun 29, 2025
TOGURI MUSEUM OF ART
At the open studio event, seven kilns opened their manufacturing sites to the public. It was a rare opportunity to get a close look at manufacturing processes that are not usually open to the public. Here, we would like to introduce the scenes from the open studio event at three of these kilns.
The main venue featured not only the usual exhibition of the manufacturing process but also a panel exhibition and presentation by students studying regional development at Nagasaki International University on the theme of “Charm and Challenges of Arita as Seen from a Student’s Perspective.” This event seemed to be meaningful and fruitful for both participants and kilns. The craftsmanship in Imari and Arita faces numerous challenges, and some issues cannot be solved solely within the production area. By involving various people and addressing challenges earnestly alongside creators, it is likely to contribute to a future that extends beyond the immediate region. The ongoing evolution of NEXTRAD’s activities is something to watch in the coming years.
Written by Kyoko Tsutsumi
Related information
NEXTRAD Official Website: https://nextrad.jp/ (JP only)