Tobe
Editor's Column "Craft Production Regions" VOL.4 AD
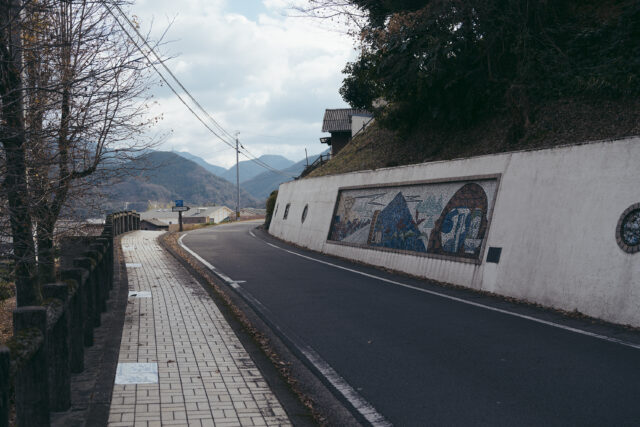
VOL.1-4
Update
VOL.1-19
Update
VOL.1-17
Update
VOL.1-43
Update
VOL.1-2
Update
VOL.1-3
Update
VOL.1
Update
VOL.1-7
Update
VOL.1-32
Update
VOL.1-26
Update
VOL.1-12
Update
VOL.1
Update
We share a variety of information and perspectives on Japanese crafts, including exhibition information and interviews.
Editor's Column "Craft Production Regions" VOL.4 AD
KOGEI Topics VOL.19
New Products VOL.17
Featured Exhibitions & Events VOL.43
Apr 5 – Jun 22, 2025
SEIKADO BUNKO ART MUSEUM
Apr 8 – May 6, 2025
The Gotoh Museum
Apr 11 – Jun 15, 2025
Kyoto City KYOCERA Museum of Art
Apr 12 – Jun 29, 2025
TOGURI MUSEUM OF ART
“Kokura-ori” was the specialty of the Buzen Kokura clan during the early Edo period – known today as Kitakyushu City in Fukuoka Prefecture. The textile, which features a three-dimensional gradation of vertical stripes, was mainly used in the making of hakama (a long-pleated wide pants worn over the kimono) and obi (a broad sash for the kimono) for the samurai. Its reputation spread throughout Japan because of the sturdiness of the material. However, the production of Kokura-ori ceased in the early Showa period. A textile artist, Ms. Noriko Tsuiki found an antique fabric swatch by chance and after scrutinizing the fabric and through a series of trial and error she was able to reproduce it. Finally, in 1984 she succeeded in reviving Kokura-ori. With the hope that more people will like Kokura-ori, she tried to make a wider fabric for general purpose. Although it is a difficult fabric to produce even through hand weaving, Ms. Tsuiki was able to successfully transfer the technique to a wide-format machine loom. The brand “KOKURA SHIMA SHIMA” by KOKURA SHIMA SHIMA INC. which is headed by Ms. Hideko Watanabe who is Ms. Noriko Tsuiki’s younger sister undertakes the mass production of the wider machine loom version of Kokura-ori.
Kokura-ori is a plain weave fabric using good quality dyed cotton thread. The fine thread woven at high density is not only soft and smooth but very strong that it was once said that “no spear can go through it”. The beautiful fabric with its vertical stripes creating a comfortable rhythm has a unique method of production being the number of warps. Kokura-ori is woven by three warps and one weft. The higher density warps which overlap the weft create the gentle gradation of stripes and colors. Apart from the density of warp, the fine thread called “rokumaru-so” used in Kokura-ori contributes to the smoothness of the fabric. The longer it is used, the more lustrous it becomes and interestingly develops a leather-like tactile. The characteristics of its aging is one of the appeals of Kokura-ori. Even though it is mass produced by machine looms, the excellent techniques of artisans are still required in case the warp is broken due to the difficult high density weaving and fine threads. Therefore, it is still the same as artisans’ works because much effort and care are needed throughout the production process.
Since the foundation of the brand “KOKURA SHIMA SHIMA”, Kokura-ori has been exhibited in overseas trade shows such as Ambiente in Germany, Maison et Objet in France, and Milan Design Week in Italy and has acquired good reputations internationally. In 2010, “KOKURA SHIMA SHIMA Furoshiki” (furoshiki is a Japanese wrapping cloth)” received the Good Design Award. In addition to the variety of fashion products, the brand has received increased demand from the interior and architecture industries. In order to push ahead towards further expansion, they started their own factory in 2018 by establishing Kokura Textile Inc. helmed by CEO, Ms. Mio Tsuiki, which deals with the production control of Kokura-ori. “KOKURA SHIMA SHIMA” continues to evolve to fit Kokura-ori into the contemporary life style and the world is paying attention to their growth.