Tobe
Editor's Column "Craft Production Regions" VOL.4 AD
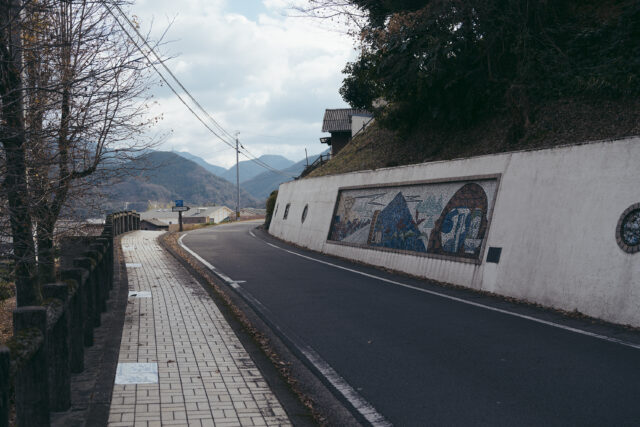
VOL.1-4
Update
VOL.1-19
Update
VOL.1-17
Update
VOL.1-43
Update
VOL.1-2
Update
VOL.1-3
Update
VOL.1
Update
VOL.1-7
Update
VOL.1-32
Update
VOL.1-26
Update
VOL.1-12
Update
VOL.1
Update
We share a variety of information and perspectives on Japanese crafts, including exhibition information and interviews.
Editor's Column "Craft Production Regions" VOL.4 AD
KOGEI Topics VOL.19
New Products VOL.17
Featured Exhibitions & Events VOL.43
Apr 5 – Jun 22, 2025
SEIKADO BUNKO ART MUSEUM
Apr 8 – May 6, 2025
The Gotoh Museum
Apr 11 – Jun 15, 2025
Kyoto City KYOCERA Museum of Art
Apr 12 – Jun 29, 2025
TOGURI MUSEUM OF ART
The establishment of Kichiemon Porcelain Co., Ltd. goes back to the Edo period or 17th century when the production of porcelain started in Arita, Saga Prefecture. They were producing sake decanter in the beginning and became recognized as a venerable kiln as it was said that the head of family was permitted to wear swords, which means that he was granted special privileges. During a certain period in the past, the kiln had stopped firing but the grandfather of Mr. Yoshiyasu Harada, the current president of the company, resumed production of porcelain in 1950, right after the war. Since then, they have made tableware for restaurants and inns and was able to differentiate themselves from other manufacturers in Arita with their colorful products realized by a special way of glazing. To further increase the company’s value, Mr. Yoshiyasu Harada developed a novel decorative technique named “Awagesho (foamy embellishment)” based on the existing technique of “Itchin” that his grandfather had used.
“Itchin” or glaze trailing is a technique of adding raised decoration on the surface of the ceramic body by squeezing out the glaze. At Kichiemon Porcelain, they have always formulated their own glaze and rich colors. Subsequently, Mr. Yoshiyasu Harada developed a technique to apply foamy glaze to the surface of porcelain after 10 years of experiment. The markings formed by popping bubbles remain even after firing resulting in unique patterns on the surface of products.
Mr. Yoshiyasu Harada explained that he had used his experienced in metal casting during his university days to develop his Awagesho technique. He had struggled to create the effect that he wanted and eventually succeeded through perseverance, inventiveness, and an inquisitive mind. Mr. Harada continues his search for new methods of embellishment as he looks towards the next stage of Arita ware which combines inherited techniques with new values. With a theme of “deconstruct and reconstruct of what is present” Kichiemon Porcelain continues their pursuit in creating new products while being mindful of their heritage. Just as they are expanding the potentials of Arita ware, at the same time their creation are adorning dining tables everywhere.